Aluminum powder is an attractive fuel, especially for micropropulsion, due to its wide availability, high volumetric and gravimetric energy densities, and environmental friendliness. For safety reasons, the powder is preferably stored and supplied to a combustion chamber separately from the oxidizer. However, powder supply systems for micropropulsion applications are technologically immature. To improve this situation, a powder supply system was developed, and the impacts of important design factors on the supply characteristics were studied. This included operating modes, carrier gas pressures, gas line conductances, and powder line lengths. The results showed that, when compared to continuous operation, pulsed operation achieved 1) significantly higher powder flow rates and 2) significantly higher ratios of powder to carrier gas mass flow rates, ϕ. Furthermore, higher carrier gas pressures can increase the powder mass flow rates, but this reduces ϕ. The gas line conductance had a lesser impact on the powder flow rates than the pressure, but increasing the former also increased the powder flow rates without significant impact on ϕ. The powder line length had a negative impact on the powder flow rate, but no significant impact on ϕ. These results will help the future development of micropropulsion systems that use powder fuels.
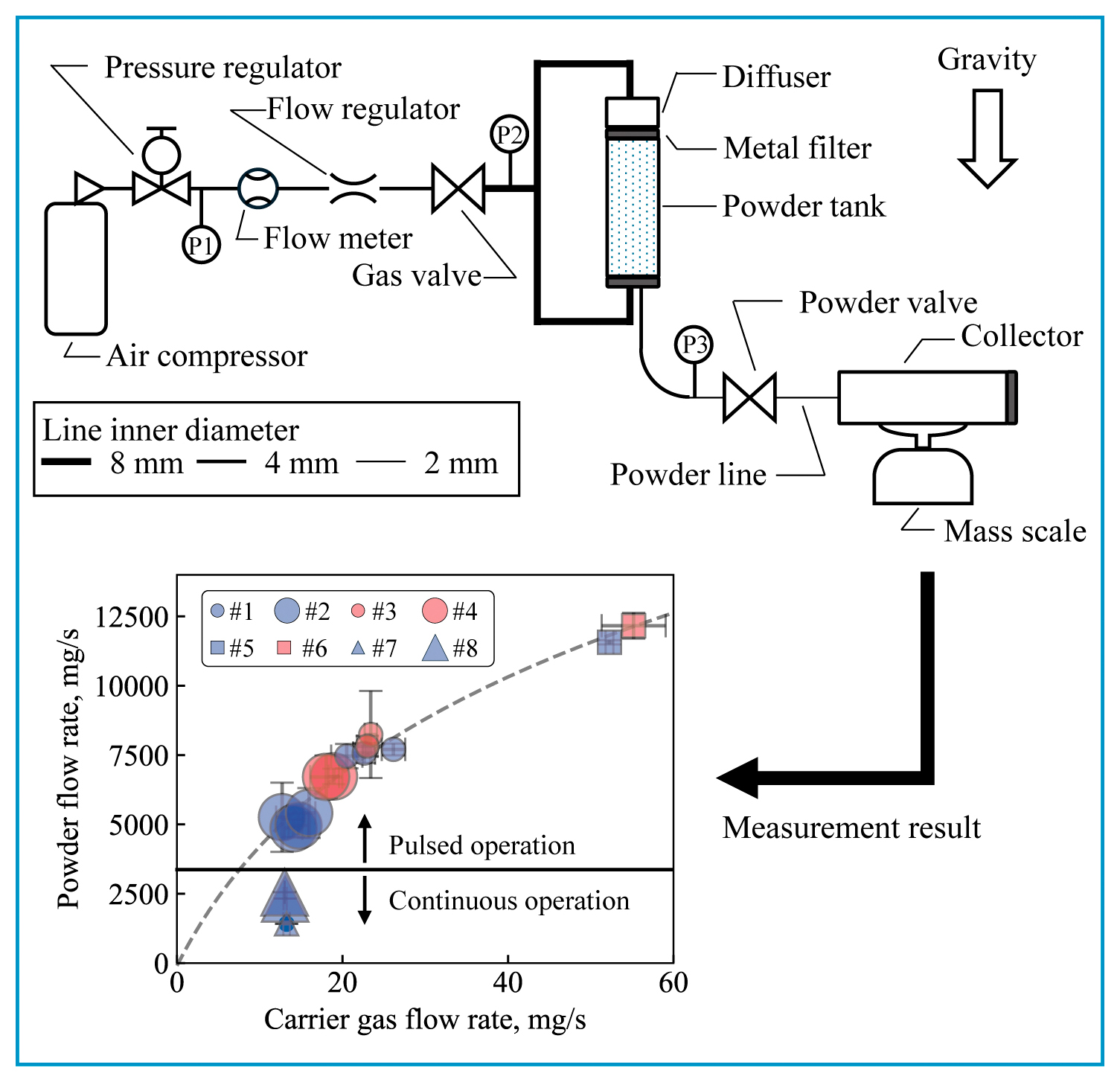
View full abstract