Special Issue on "Recent Approaches to Control of Cohesive Zone Phenomena and Improvement of Permeability in Blast Furnace"
-
Hiroshi Nogami
Article type: Preface
2020 Volume 60 Issue 7 Pages
1379
Published: July 15, 2020
Released on J-STAGE: July 16, 2020
JOURNAL
OPEN ACCESS
FULL-TEXT HTML
-
Shigeru Ueda, Takahiro Miki, Sun-Joong Kim, Xu Gao, Hiroshi Nogami, Sh ...
Article type: Regular Article
2020 Volume 60 Issue 7 Pages
1380-1388
Published: July 15, 2020
Released on J-STAGE: July 16, 2020
JOURNAL
OPEN ACCESS
FULL-TEXT HTML
In this study, we analyze the softening and melting behaviors of the CaO–FeO–SiO2–Al2O3–MgO system for improving gas permeability in a blast furnace. The temperature of the oxide is increased to 1723 or 1773 K in a CO/CO2 mixture; the softening and melting temperatures and the temperature of penetration into the coke bed are measured. Because the CO/CO2 ratio in the atmosphere influences the stable state of iron or iron oxide, the softening and melting behaviors are investigated for numerous CO/CO2 ratios. We observe that the reduction of the sample progresses in an atmosphere with a high CO/CO2 ratio, and thus, the softening temperature increases. Because the composition of the oxidation phase influences the solidus and liquidus temperatures, the influence of basicity on the phenomena is also investigated, and a method of reducing the difference between the softening and dripping temperatures is discussed.
View full abstract
-
Yasushi Ogasawara, Takeshi Sato, Jun Ishii, Ryota Murai, Shiro Watakab ...
Article type: Regular Article
2020 Volume 60 Issue 7 Pages
1389-1394
Published: July 15, 2020
Released on J-STAGE: July 16, 2020
JOURNAL
OPEN ACCESS
FULL-TEXT HTML
Return fines of sinter were agglomerated with a binder material such as cement and fine powder of blast furnace slag in order to use the agglomerates as raw materials in the blast furnace. Reduction tests of the agglomerates were carried out to investigate the high temperature properties of the agglomerates. The following findings were obtained. The agglomerates have lower RDI (RDI<20%) than sinter because sinter, which consists of brittle glassy silicate, was arranged discretely in the agglomerates and bonded by the soft materials of the binder, and as a result, size degradation during reduction was prevented. The agglomerates have higher RI (DI>70%) than sinter due to the high abundance ratio of fine pores in the agglomerates. Moreover, in comparison with sinter, the agglomerates also have equal or greater strength after reduction at 700°C and 900°C because solid phase sintering was promoted by adding ultrafine iron oxide powder. Therefore, as a blast furnace raw material, the permeability and reducibility of the agglomerates of return fines of sinter are superior to those of conventional sinter. This concept is considered to be effective for utilizing sinter fines as blast furnace raw materials in a high pulverized coal rate and low coke rate operation.
View full abstract
-
Yuki Kawashiri, Taihei Nouchi, Hidetoshi Matsuno
Article type: Regular Article
2020 Volume 60 Issue 7 Pages
1395-1400
Published: July 15, 2020
Released on J-STAGE: July 16, 2020
JOURNAL
OPEN ACCESS
FULL-TEXT HTML
Recently, demands for reduction of CO2 gas emission in iron making process are increasing. For further reduction of CO2 gas emission, a method of capturing carbon dioxide from blast furnace exhaust gas has been studied. The oxygen blast furnace using pure oxygen for blast does not contain nitrogen in the exhaust gas and that is more advantageous than conventional blast furnace in the point of view of CO2 separation energy. Although the oxygen blast furnace has been studied with the experimental furnace, the experimental furnace was not sufficiently investigated on the properties of cohesive layer because of the small load of burden materials. Therefore, in this study, the properties of cohesive layer of the oxygen blast furnace were studied.
The properties of the cohesive layer were evaluated under blast furnace conditions and nitrogen-less conditions in a load-softening test. As a result, the properties of cohesive layer were remarkably improved in nitrogen-less conditions. As a result of discussion, improvement of the properties of cohesive layer was quantitatively explained due to suppression of contraction of the sintered ore and the decrease of slag liquid because the nitrogen-less atmosphere promoted reduction reaction.
View full abstract
-
Shinsuke Ogyu, Lichun Zheng, Xu Gao, Shigeru Ueda, Sohei Sukenaga, Shi ...
Article type: Regular Article
2020 Volume 60 Issue 7 Pages
1401-1408
Published: July 15, 2020
Released on J-STAGE: July 16, 2020
JOURNAL
OPEN ACCESS
FULL-TEXT HTML
To enhance the descent of droplets in the coke bed of a blast furnace, the sliding angle of the water droplet and the advancing and receding contact angles at the time of sliding were measured. Coke used as a reducing agent in a blast furnace was employed as a substrate. Because the shape of the coke surface varies with the gasification reaction with CO2, the coke substrate was treated with heat (1273 K) in a CO/CO2 atmosphere. Irregularities of approximately several micrometers were formed on the coke surface by the gasification reaction, and the sliding angle of the droplet decreased.
View full abstract
-
Kai Zhou, Jiaqi Song, Zhixiong You, Hongen Xie, Xuewei Lv
Article type: Regular Article
2020 Volume 60 Issue 7 Pages
1409-1415
Published: July 15, 2020
Released on J-STAGE: July 16, 2020
Advance online publication: March 20, 2020
JOURNAL
OPEN ACCESS
FULL-TEXT HTML
Vanadium–titanium magnetite (VTM) is an important strategic resource, and now the process of Blast Furnace (BF) is the dominate route for smelting VTM. However, the difficulties of smelting VTM by BF inhibited further increase of VTM proportion in furnace burden due to its complex behavior in cohesive zone. The objective of this study is to reveal the softening–melting behavior of a high titanium sinter. The results indicated that the softening–melting properties of the experimental high titanium sinter were relatively worse than that of ordinary sinter due to its wider melting temperature interval and bad gas permeability in melting stage. The melting temperature interval of 225°C was obtained, and the permeability index (S value) of 1917 kPa·°C was calculated correspondingly. A second increase in pressure drop was observed in the softening–melting process, which may be ascribed to great difference of melting point between pig iron and slag. The mechanism on slag evolution was also clarified by interrupting the softening–melting process at characteristic temperatures. The XRD patterns indicated that initial slag phase mainly consisted of wustite, silicates and perovskite, of which the wustite content decreased gradually during the softening–melting process. The content of wustite was a crucial factor that affected the phase transformation during slag evolution.
View full abstract
-
Subhasish Mitra, Xinliang Liu, Tom Honeyands, Geoffrey Evans, Damien O ...
Article type: Regular Article
2020 Volume 60 Issue 7 Pages
1416-1426
Published: July 15, 2020
Released on J-STAGE: July 16, 2020
Advance online publication: March 20, 2020
JOURNAL
OPEN ACCESS
FULL-TEXT HTML
The softening and melting (SM) under load test is routinely conducted to assess the quality of ferrous burden materials and to predict their possible performance in blast furnace. Due to complex phase interactions coupled with chemical reactions at an elevated temperature range (~973 to 1873 K), the flow dynamics in the test system are quite complex. This study systematically investigates the contraction behaviour and associated pressure drop in a SM test bed for sinter, lump (NBLL, Newman Blend Lump) and a mixture of these two types of ore (21 wt% NBLL + 79 wt% sinter). To quantify the structural changes in a sample bed, interrupted tests at various temperatures were conducted and analysed using both synchrotron X-ray computed tomography (CT) at a lower temperature range (1273 to 1473 K) and neutron CT at a higher temperature (1723 K). It was noted that existing packed bed pressure drop models (Ergun model, 1952, fused bed model, Sugiyama et al., 1980, orifice model, Sugiyama et al., 1980) and modified orifice model, Ichikawa et al., 2015) exhibited divergence in their predictions at higher temperature when the porosity parameter was computed directly from the bed contraction data. To avoid this modelling failure, a growth-decay type porosity-temperature relationship based on extensive SM test data was incorporated in the well-known Ergun equation which estimated reasonable bed pressure drops. Furthermore, a simplified ore specific friction factor model was empirically derived which was also shown to produce reasonable pressure drop predictions for all types of ferrous burden samples.
View full abstract
-
Yasuaki Ueki, Koki Teshima, Ryo Yoshiie, Ichiro Naruse
Article type: Regular Article
2020 Volume 60 Issue 7 Pages
1427-1433
Published: July 15, 2020
Released on J-STAGE: July 16, 2020
JOURNAL
OPEN ACCESS
FULL-TEXT HTML
A significant amount of CO2 gas is emitted from blast furnaces in ironmaking processes because large amounts of coke and pulverized coal are consumed as the reducing agent and heat source. Accordingly, CO2 emissions from blast furnaces should be reduced to control global warming. One promising method to achieve the CO2 reduction involves decreasing the reducing agent rate (RAR) during blast furnace operation. However, fine particles such as ash, derived from coke and pulverized coal, may affect the permeability in the furnace under low RAR operation. Therefore, the behavior of ash particles in a coke lump during combustion and gasification was elucidated experimentally in this work. Combustion and gasification experiments on a single coke lump were conducted in air and in a CO–CO2 gas mixture atmosphere at temperatures from 1473 to 1673 K. The ash particles in the coke lump were observed using a scanning electron microscope (SEM). Many large ash particles were observed near the surface of the coke lump during combustion. This is because the ash particles coalesced with the neighboring ash particles near the surface. Only molten fine ash particles were formed during gasification. This difference in the ash behavior during combustion from gasification will depend on the consumption behavior of the carbonaceous matrix.
View full abstract
-
Takahiro Miki, Akito Kawakami
Article type: Regular Article
2020 Volume 60 Issue 7 Pages
1434-1437
Published: July 15, 2020
Released on J-STAGE: July 16, 2020
JOURNAL
OPEN ACCESS
FULL-TEXT HTML
Generally, reactions and forming phases during ironmaking can be thermodynamically predicted using equilibrium phase diagram. However, at low temperature it will likely to be different from predicted phases and deviate from equilibrium. Hence, knowledge of solid state reaction at low temperature is required to control the melting behavior of slag phase in blast furnace. Formation of 2CaO·SiO2 by the reaction between gangue SiO2 and liquid CaO–FeO phase will give negative effect to molten slag formation during ironmaking process, and enhancing the dissolution of SiO2 into CaO–FeO liquid phase is crucial.
It was found that 2CaO·SiO2 phase layer formed at the interface between SiO2 and CaO–FeO melt by rapidly heating the sample to 1423 K. Dissolution of SiO2 into CaO–FeO melt was enhanced by Al2O3 addition to the CaO–FeO melt. When the sample was rapidly heated to 1473 K, formation of 2CaO·SiO2 was not observed and the dissolution of SiO2 into CaO–FeO liquid phase was significant. Rapid heating to 1473 K will avoid formation of 2CaO·SiO2 phase and enhance melting of gangue minerals to form liquid slag.
View full abstract
-
Masahiro Yakeya, Akito Kasai, Rikizo Tadai, Kentaro Nozawa
Article type: Regular Article
2020 Volume 60 Issue 7 Pages
1438-1444
Published: July 15, 2020
Released on J-STAGE: July 16, 2020
JOURNAL
OPEN ACCESS
FULL-TEXT HTML
A major operational problem in increasing pulverized coal rate and decreasing coke rate must be the increased pressure drop or the worsened gas permeability at the lower part of the blast furnace. In order to decrease the pressure drop at the blast furnace cohesive zone (CZ) under low coke rate operation, this study has focused on mixed coke charging in the ore layer. Results obtained by numerical analysis and experiments are as follows:
(1) Numerical analysis using DEM (Discrete Element Method) clarified the change in the cohesive ore bed structure with mixed coke charging and the formation conditions of gas path in the bed. Also, DEM-CFD (DEM and Computational Fluid Dynamics) analysis enabled us to find a gas permeability improvement mechanism and an optimum coke mixing ratio for different CZ conditions before applying the technology.
(2) Experiments in blast furnace hot model demonstrated the decreased pressure drop at the CZ by mixed coke charging in the ore layer. The experimental results abided by the numerical analysis results.
View full abstract
-
Shungo Natsui, Akinori Sawada, Hiroshi Nogami, Tatsuya Kikuchi, Ryosuk ...
Article type: Regular Article
2020 Volume 60 Issue 7 Pages
1445-1452
Published: July 15, 2020
Released on J-STAGE: July 16, 2020
JOURNAL
OPEN ACCESS
FULL-TEXT HTML
A simulation of the dripping behavior of solid-phase suspended molten slag in a coke bed was performed using the Bingham fluid model in the framework of smoothed particle hydrodynamics (SPH). SPH can track the motion of droplets which are suspended in dispersed solids. A case study was performed in which the yield coefficient varied with the viscosity coefficient of the molten SiO2–CaO–Al2O3 slag, with suspended solids approximated by the Bingham fluid model, and the holdup droplets were trapped at approximately the same site regardless of the yield value. When the yield value exceeded the threshold, the volume of each holdup droplet increased. This threshold is correlated with the decrease in the shear rate at the bottleneck. Increasing the solid phase ratio in the molten slag is also predicted to increase the yield value with viscosity; thus, the amount of holdup droplets increases at the specific holdup sites as a dispersed phase. This indicates that the increase in the yield value approaches the powder holdup mechanism that is closed one after another starting from a specific holdup site.

View full abstract
-
Shungo Natsui, Akinori Sawada, Hiroshi Nogami, Tatsuya Kikuchi, Ryosuk ...
Article type: Regular Article
2020 Volume 60 Issue 7 Pages
1453-1460
Published: July 15, 2020
Released on J-STAGE: July 16, 2020
JOURNAL
OPEN ACCESS
FULL-TEXT HTML
This study attempted to conduct a topological data analysis of groups of particles in packed-bed structures to provide quantitative evaluations of void shapes. This study examined the spatial correlation between the packed bed structure and the holdup sites through geometric data obtained from the coordinates of the various particles composing the packed bed to isolate characteristic structural data for liquid holdup sites in a packed bed. When the study defined “bottlenecks” as narrow areas of a scale below capillary length, it was discovered that, in packed beds consisting of particles of a single diameter, the contribution to holdup was related to the number density of bottlenecks. Regarding the dependence on the void fraction of the holdup sites, as trends were demonstrated that differed from the continuous change that accompanies changes in the modified Capillary number, the difference from the dimensionless correlation occurs. When particles of differing diameters intermingle, the bottleneck number density increases near particles with small diameter, and the percentage of blockages from droplets increases. As position and density differ depending on the particle packing method, it is suggested that holdup sites decrease in number when particles with small diameter are appropriately dispersed.

View full abstract
-
Yanan Lu, Shengli Wu, Binbin Du, Heng Zhou
Article type: Regular Article
2020 Volume 60 Issue 7 Pages
1461-1468
Published: July 15, 2020
Released on J-STAGE: July 16, 2020
JOURNAL
OPEN ACCESS
FULL-TEXT HTML
As for ferrous burden, the softening and melting (SM) behaviors greatly affect the cohesive zone thickness, position and shape. Ironmaking researchers have found that it’s not appropriate to evaluate the blast furnace burdens only based on the SM behavior of single iron-bearing materials because the sinter will interact with acid materials at high temperatures. In present study, a new visual method has been given to research the SM behavior of five single iron ores and four types of mixed burdens. The results show that the SM properties of all iron ores in the cohesive zone (CZ) are enhanced through interactions at high temperature. Due to intense interaction at high temperature, SM behavior of the mixture burden A (containing lump ore L-A and sinter) is better than the mixture burden B (containing lump L-B and sinter), despite the lump ore L-A SM behavior is remarkably reduced compared with the lump ore L-B. Additionally, experimental results for melting and dropping of integrated burdens also prove that high temperature interaction is important for enhancing the performance of SM in ferrous materials and improving the permeability of the blast furnace.
View full abstract
-
Shingo Ishihara, Junya Kano
Article type: Regular Article
2020 Volume 60 Issue 7 Pages
1469-1478
Published: July 15, 2020
Released on J-STAGE: July 16, 2020
JOURNAL
OPEN ACCESS
FULL-TEXT HTML
A new simulation model for the analysis of solid to liquid phase transition behaviors inside the blast furnace was developed in this study. The solid state is treated by ADEM (Advanced Distinct Element Method) and the liquid state is treated by SPH (Smoothed particle Hydrodynamics). The intermediate state is treated by overlapped calculation of both ADEM and SPH. Numerical examinations for the analysis of several phenomena such as dam brake flow, droplet deformation due to the contact angle and phase transition were performed. The validity of the proposed model was confirmed by comparison with the experimental results of the motion of the leading edge in collapse of a water column in the dam break test. The phase transition behavior of ore was observed experimentally using horizontal furnace. The deformation started at about 1200°C from the upper corner of sample pellet became round, and melted down to the whole with slight contraction. A similar behavior is also can be seen in the simulation by appropriately setting the relationship between the temperature and the joint spring coefficient. These results are indicated that the developed model has possibility to clarify the burdens behavior including the phase transition inside the blast furnace.

View full abstract
-
Kengo Kato, Hirokazu Konishi, Hideki Ono, Shinji Fujimoto, Yuichiro Ko ...
Article type: Regular Article
2020 Volume 60 Issue 7 Pages
1479-1486
Published: July 15, 2020
Released on J-STAGE: July 16, 2020
JOURNAL
OPEN ACCESS
FULL-TEXT HTML
Reduction experiments were conducted with sintered Fe2O3–CaO–SiO2–Al2O3 tablets at (mass%CaO)/(mass%SiO2) (C/S) of 1.5, 2.0, and 2.5 at 1000, 1050, 1100, 1150, and 1200°C. From the reduction behaviors, we investigated the relationship between the reduction rate and C/S at the softening and melting zone temperatures of blast furnaces. The reduction rates at C/S = 2.0 and 2.5 increased with temperature in the range of 1000 to 1200°C. The reduction rate at C/S = 1.5 increased with temperature in the range of 1000 to 1150°C; however, at 1200°C, it decreased to the same value obtained at 1000°C. The microstructures of these samples, after sintering at 1270°C, pre-reduction at 900°C, and reduction at 1200°C, were analyzed through SEM-EDS. Fe2O3 particles, SFCA, slag, and pores among Fe2O3 particles existed in the samples after sintering. The matrix components in the pre-reduced sample were suggested to be calcium silicate slag containing FeOx and Al2O3 at C/S = 1.5, and to be ‘FeOx’ originated from SFCA at C/S = 2.0 and 2.5. The porosity of the open pores at C/S = 1.5 decreased to 16%. It was found that the reduction rate at 1200°C decreased due to this lower porosity. By contrast, the porosity of the open pores after reduction at C/S = 2.0 and 2.5 was much higher than that after pre-reduction. The reduction rates of these samples at 1200°C were found to not decrease as a result of maintaining a higher porosity.
View full abstract
-
Naoto Yasuda, Koki Nishioka, Seiji Nomura
Article type: Regular Article
2020 Volume 60 Issue 7 Pages
1487-1494
Published: July 15, 2020
Released on J-STAGE: July 16, 2020
JOURNAL
OPEN ACCESS
FULL-TEXT HTML
In order to clear shrinkage behavior of sinter during softening process, the effects of load and reducing gas condition on the shrinkage rate of sinter packed bed has been investigated using an experimental apparatus for measuring high temperature properties under load. As a result, the shrinkage rate increased with increasing the load impressed to the packed bed in temperature range from 1270 to 1440 K, and decreased with increasing the reduction degree of sinter in temperature range from 1470 to 1570 K. The results indicate that the mechanism of shrinkage was different depending on temperature.
In this study, the shrinkage rate of sinter was formulated by dividing into two temperature regions. In the region I, the shrinkage rate increased in proportional to the impressed load, and increased in inversely proportional to the apparent softening viscosity. In the region II, the shrinkage rate increased in proportion to the generation rate of melt, and decreased with increasing the volume fraction of metallic iron in the packed bed. The shrinkage in region II was suppressed with increasing the reduction degree of sinter since the generation rate of melt decreased and the volume fraction of metallic iron increased. The shrinkage rate of each region was expressed as functions of initial composition of sinter, load, temperature, and reduction degree. The calculated values were in good agreement with the experimental ones.
View full abstract
-
Hiroshi Nogami
Article type: Regular Article
2020 Volume 60 Issue 7 Pages
1495-1503
Published: July 15, 2020
Released on J-STAGE: July 16, 2020
Advance online publication: May 11, 2020
JOURNAL
OPEN ACCESS
FULL-TEXT HTML
The cohesive zone of the blast furnace is one of the most important zones because it deeply relates to the furnace stability and efficiency. It is considered that the thickness of the cohesive zone increases with decreasing the reducing agent rate and increasing the usage of the low grade raw materials in future. The thickness of the cohesive zone should be decreased or permeability of the cohesive zone should be improved to keep the furnace stability and production efficiency. Heat transfer in the cohesive zone is a quite important issue to control the cohesive zone because it determines the temperature rise of this zone namely softening and melting rate of the burden materials. In this study, a mathematical simulation model for the fluid flow and heat transfer in the packed bed of the deforming particles was developed. This model combined the discrete element method for bed deformation and the computational fluid dynamics for the gas flow. Additionally, the inter-particle heat exchange in the deforming packed bed was newly formulated and linked with the discrete element analysis. This mathematical model successfully revealed the variation of the heat transfer mechanism with the deformation of the packed bed. The simulation results could give the useful information for designing the burden distribution under the low carbon and high low-grade material operation of the blast furnace.

View full abstract
-
Shengli Wu, Yanan Lu, Zhibin Hong, Heng Zhou
Article type: Regular Article
2020 Volume 60 Issue 7 Pages
1504-1511
Published: July 15, 2020
Released on J-STAGE: July 16, 2020
JOURNAL
OPEN ACCESS
FULL-TEXT HTML
In order to solve the problem of poor gas permeability of blast furnace caused by high Al2O3 content in the burden, the softening and melting properties of sinter, pellets and lump ores are studied in this paper. The results show the differences between acid and basic iron ore materials. Based on this, this article study the influence of different kinds of pellets and lump ores blending with sinter on the softening and melting properties of comprehensive burdens. The results show that the self-fluxing pellet and porous lump ore with high aluminium content caused the Al2O3 content of comprehensive burden to raise 0.26% compared to acid pellet and dense lump ore with low aluminium content. However, the highest pressure drop of comprehensive burden is reduced from 2.50 kPa to 1.70 kPa, the S-value is decreased from 198 kPa∙°C to 114 kPa∙°C. Therefore, this method of ore blending will improve the softening and melting properties of integrated burden.
View full abstract
-
Ko-ichiro Ohno, Yoshiki Kitamura, Sohei Sukenaga, Sungo Natsui, Takayu ...
Article type: Regular Article
2020 Volume 60 Issue 7 Pages
1512-1519
Published: July 15, 2020
Released on J-STAGE: July 16, 2020
JOURNAL
OPEN ACCESS
FULL-TEXT HTML
Negative effect from low coke rate operation at cohesive zone is obvious because it makes thinning of coke slit thickness. Correct knowledge about gas permeability of cohesive layer is becoming more and more important. In order to precisely understand cohesive behaviour, a softening and melting simulator under rapid heating and quenching conditions was applied for clarify a determinant factor of gas permeability behaviour. To focus on softening and melting behaviour, granulated slag particle bed layer without iron oxide was prepared as packed bed sample layer can show softening and melting. The packed bed slag samples in graphite crucible were rapidly heated up to 1200°C, and then gradually heated up to 1500°C with 10°C/min under inert gas atmosphere and 0.1 MPa load. Gas pressure drop and shrinkage degree of the sample layer were measured during the softening and melting test, and quenched sample was made at certain temperature when the maximum gas pressure drop was measured. The CT observation of the quenched sample provided 3D shape information of gas path shape in sample packed bed. Gas pressure drop was estimated with fanning’s equation with the gas path information. The estimation values were shown positive correlation with measured maximum pressure drop. The CT observation also gave triple line length among molten slag, graphite, and gas. Combination the triple line length and molten slag surface tension could use for evaluation of static force balance when maximum pressure drop obtained.

View full abstract
-
Ko-ichiro Ohno, Hirokazu Konishi, Takashi Watanabe, Shingo Ishihara, S ...
Article type: Regular Article
2020 Volume 60 Issue 7 Pages
1520-1527
Published: July 15, 2020
Released on J-STAGE: July 16, 2020
JOURNAL
OPEN ACCESS
FULL-TEXT HTML
Reduction test under load is normally applied to evaluate softening and melting behaviour of ferrous burdens at simulated condition in cohesive zone in blast furnace. Outcomes from this test are very complex because they depend on reduction degree, chemical composition, basicity, melts physical property, etc. One of the reasons to make complex this test is sample for the test provided as particle packed bed. In order to comprehend softening and melting behaviour of cohesive zone, focus on behaviour of single particle as a component of particle packed bed in this study. For simplification, a pre-reduced simulant sinter iron ore was prepared as single tablet sample. The samples were made from mixture of reagent oxides and they were pre-reduced to control their reduction degree to several reduction levels. The tablet sample was rapidly heated up to 900°C, and then gradually heated up with 10°C/min under inert gas atmosphere and 0.1 MPa load. Shrinkage degree of the sample was measured during the softening and melting test, and quenched sample was made at certain temperature when the sample shows a characteristic tendency. Cross-sectioning observation of the quenched sample provided mineral phases distribution in the tablet sample. The observation indicated that peripheral structure has a significant effect on deformation resistance. Especially in there, existence of molten slag phase could make easy to deform the sample particle shape, and metallic solid Fe phase helped to strengthen the particle’s deformation resistance.
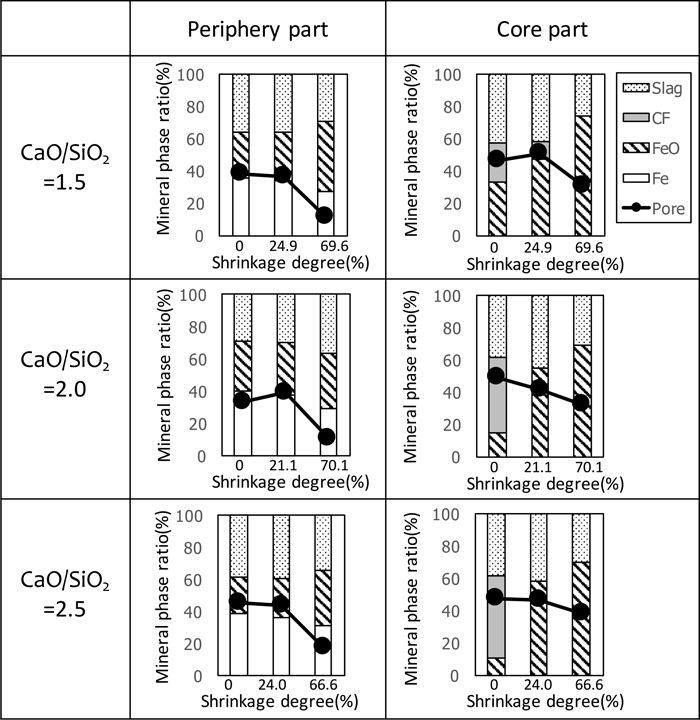
View full abstract
-
Siahaan Andrey Stephan, Yoshihiko Oishi, Hideki Kawai, Hiroshi Nogami
Article type: Regular Article
2020 Volume 60 Issue 7 Pages
1528-1537
Published: July 15, 2020
Released on J-STAGE: July 16, 2020
JOURNAL
OPEN ACCESS
FULL-TEXT HTML
Under low reducing agent rate and high pulverized-coal injection rate operations, coke powder and unburnt char are generated in the blast furnace. These powders flow through the packed bed inside the furnace entrained by the gas flow. The powders accumulation in packed bed will deteriorate gas and liquid permeability and creates an unstable situation inside the blast furnace. Thus, it is important to quantitatively evaluate the accumulation rate on a distribution channel of coke powders. In this study, the behavior of the powder particles passing through the orifice formed by three coarse particles that osculate one another and compound in an equilateral triangle was numerically analyzed using the DEM-CFD. The results revealed the effect of drag force on the powder motion passing through the orifice. Moreover, the effect of the position of the powder passing through the orifice to pressure drop fluctuation inside the triangular prism is also analyzed.
View full abstract
-
Akira Suzuki, Nobuhiro Maruoka, Yoshihiko Oishi, Hideki Kawai, Hiroshi ...
Article type: Regular Article
2020 Volume 60 Issue 7 Pages
1538-1544
Published: July 15, 2020
Released on J-STAGE: July 16, 2020
JOURNAL
OPEN ACCESS
FULL-TEXT HTML
The control of packed bed permeability in blast furnace is an important issue to realize highly efficient and stable operation of blast furnace under low carbon condition. The powder accumulation in the packed bed deteriorates the permeability, thus it is necessary to understand the powder behavior in the packed bed. Recently it was revealed that the existence of liquid in the bed had drastic effect on the motion and the accumulation of powder in the bed. In this study a mathematical model to describe the behavior of powder particle under liquid existing condition was developed using discrete element method. The model took into account cohesive force, normal viscous force, sheer viscous force and lubrication due to the liquid film. The model was validated by the comparison of the particle trajectories under various liquid properties. The model was applied to the simulation of passing behavior of the powder particles through the opening among three coarse spherical particles, and successfully reproduced the accumulation behavior under wetting condition.
View full abstract
-
Shingo Ishihara, Ko-ichiro Ohno, Hirokazu Konishi, Takashi Watanabe, S ...
Article type: Regular Article
2020 Volume 60 Issue 7 Pages
1545-1550
Published: July 15, 2020
Released on J-STAGE: July 16, 2020
JOURNAL
OPEN ACCESS
FULL-TEXT HTML
Softening and melting phenomena of burdens in the cohesive zone in the blast furnace are factors that cause the deterioration of gas permeability. Numerical examinations to predict the softening behavior of burdens in the packed bed were performed in this study. In order to represent the softening characteristics of the simulant sinter ore, the simulation of a single pellet load softening test was carried out. The strength properties of the pellets were evaluated by the shrinkage degree in the load softening test.
Shrinkage degree of pellets with different basicity and pre-reduction ratio were attempted to reproduce. To represent the softening behavior of the pellet, ADEM (Advanced Distinct Element Method) SPH (Smoothed Particle Hydrodynamics) coupling model was applied. Softening and shrinkage could be represented by decreasing the joint spring coefficient while the pellet was loaded. The relationship between the joint spring coefficient and the temperature was determined to compare the shrinkage degree obtained in the experiment and the simulation. The determined joint spring coefficient was used to predict the softening behavior in the load softening test of a packed bed. The simulation results of the shrinkage degree curve showed good agreement with the experimental results. It was indicated that the softening behavior in the cohesive zone could be predicted by this calculation method.
View full abstract
-
Shin Satou, Siahaan Andrey Stephan, Yoshihiko Oishi, Hideki Kawai, Hir ...
Article type: Regular Article
2020 Volume 60 Issue 7 Pages
1551-1559
Published: July 15, 2020
Released on J-STAGE: July 16, 2020
JOURNAL
OPEN ACCESS
FULL-TEXT HTML
As a method for reducing CO2 in blast furnaces, low-reducing agent ratio and large amount of pulverized coal is being carried out to reduce the amount of coke used and reduce the carbon input to the blast furnace and its operation cost. However, these operating methods increase the deposit amount of coke powder and unburned char generated in the blast furnace and decrease process efficiency. A three-dimensional numerical model is built and observed by the coupling system of DEM-CFD, performed to understand the principal factors that affected fine and gas permeability. Simulation is carried out in, where fine particles are injected simultaneously from the bottom of cylindrical packed bed, mimicking the experimental approach. The fine to packed diameter ration is given by 0.133≤Dp/dp≤0.162. At a larger diameter ratio, fine particles tend to concentrate at the bottom of the packed bed. In the case of lower particle diameter ratio, updraft gas will easy to permeate along with fine particles because of the existing of large open flow channels relative to fine diameter. Furthermore, no significant change in fine fraction transported to the upper area due to the change of gas velocities. In this present study, the effect of continuous fine particles injection and its effect on gas flow can be observed, where the gas flow avoiding the heavily concentrated area.
View full abstract
-
Hiroshi Nogami, Takuto Yamawaki
Article type: Regular Article
2020 Volume 60 Issue 7 Pages
1560-1569
Published: July 15, 2020
Released on J-STAGE: July 16, 2020
JOURNAL
OPEN ACCESS
FULL-TEXT HTML
The void structure in the deforming packed bed like cohesive zone of blast furnace was discussed. The examined packed bed consisted of mono-dispersed spherical particles and was numerically prepared by using the discrete element method. From the obtained packing particle structure, the characteristics of the void space, namely voidage, surface area, hydraulic radius, flow path network structure, width and length of the flow path, were extracted. The actual hydraulic radius deviated from the one calculated from the bed shrinkage with the bed deformation, and this deviation resulted the large difference in the pressure drop in the packed bed. The flow path (void) network was successfully extracted from the particle packing structure. Additionally, distributions of the path width and length were obtained. The choking of flow path with bed shrinkage can be quantitatively visualized. In the softening ore particle bed with nut coke mixing, the flow path structures around ore and nut coke particles showed different behavior. With the obtained characteristics of the void structure, the variations of the pressure drops in the reduction test under loading and in the softening ore layer with coke mixing can be explained.

Variation of pressure drop with shrinkage. (Online version in color.)
Fullsize Image
View full abstract